Sustain - The Fifth 5S
Sustaining the 5S methodology can be the most challenging aspect, depending on the nature of your business and the morale of your staff. It’s important to involve your team when implementing the other four 5S’s. This way, they will feel a sense of ownership towards their work area. If the staff is the one who put in all the hard work and effort to create a clean and organized workspace, they would be more motivated to maintain it over time.
You must get the staff in the 5S habit and follow all the rules. When they follow the rules it will be easy to audit the work areas with the checklists and standards you have set in place from the previous 4S’s. To sustain all the hard work you have done to this point, follow these steps.
Step 1 - Implement Visual Controls
The simplest method is to perform a visual inspection to determine if a work area is still in compliance with its 5S objectives. This means that if you have organized the work area effectively and assigned everything to a specific location, it will be straightforward to identify when an item is not where it should be and needs to be repositioned.
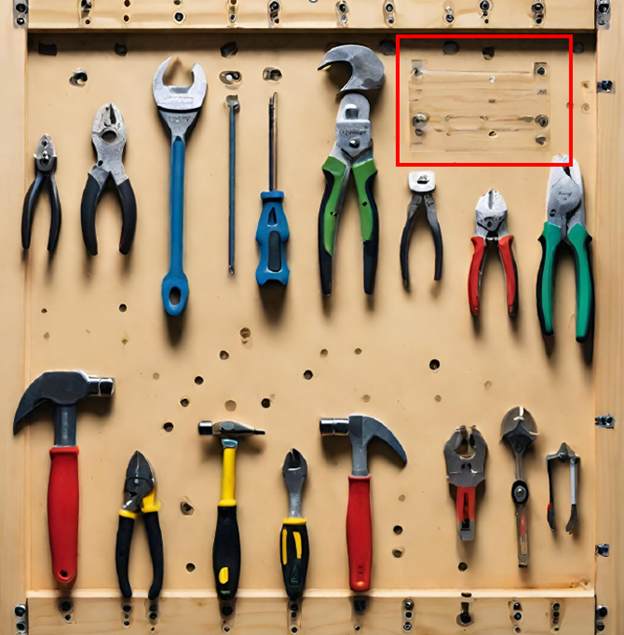
It is common for companies that implement the 5S methodology to utilize visual controls during the 5S audit process. These visual cues are intended to indicate areas that require improvement or correction of current staff behaviour in that particular area. As you progress through the next steps, you will learn more about these visual indicators and their significance in the 5S process.
Step 2 - Strive For The Showcase Work Area
Team members may sometimes feel that aiming for perfection in their work area is too high of a goal. However, it’s important to understand that a work area must only follow a few key rules to ensure it becomes a showcase work area. Having conducted numerous 5S audits, I have seen employees put in a lot of effort to achieve the perfect 5S score in their area. These individuals are proud of their work and want to ensure the auditor recognizes their hard work.
This showcase work area is not hard to achieve when you look at the items that need to be cleaned and put away in each area. We only ask team members to keep the area clean and put away all items where they were originally stored on the shelf or tool board.
Step 3 - 5S Audits
Each factory that implements 5S in their business needs to have a 5S audit schedule to make sure all areas stay as clean and organized as the first day all activities were done. In Japan, there are many audits and check sheets to create a habit in every worker to build a 5S culture.
The below audit sheet is an example of the criteria used during an audit. Every non-conformance is documented when an auditor finds an item that does not follow the standard.
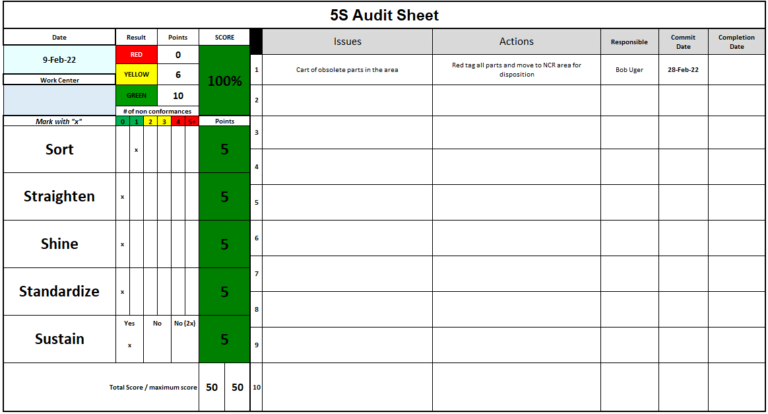
As you can see from the example 5S audit sheet, the score you choose for your 5S can be 1 to 5 or 1 to 100, but whatever scale you use, you will need to colour-code the rating. For example, 4 or 5 will give you a green, 2 or 3 will give you a yellow, and 1 will give you a red.
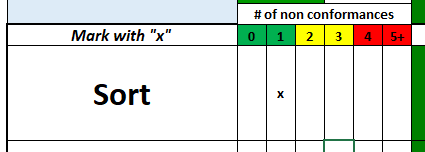
When a work area receives a YELLOW or low score during an audit, it indicates that they need to improve their performance to achieve a better score in the next audit. If the work area receives a RED, it means that immediate corrective action is required, which will be taken up by the supervisor of that area. By giving attention to the YELLOW and REDs and guiding the team to resolve the issues, they will be encouraged to keep their work area clean and organized, thus avoiding such incidents.
Step 4 - 5S Audit Tracker
We all like a little competition in our lives as long as it’s friendly. This is what the 5S Audit Tracker will do for your business. The tracker is posted around the factory and morning meeting areas so supervisors can talk about how well a team did or the improvements needed in certain work areas.
The tracker is also placed on the news bulletin board at your business so people can see how well other teams are doing compared to them. It is a great tool for supervisors to help see areas struggling and others doing well with 5S.
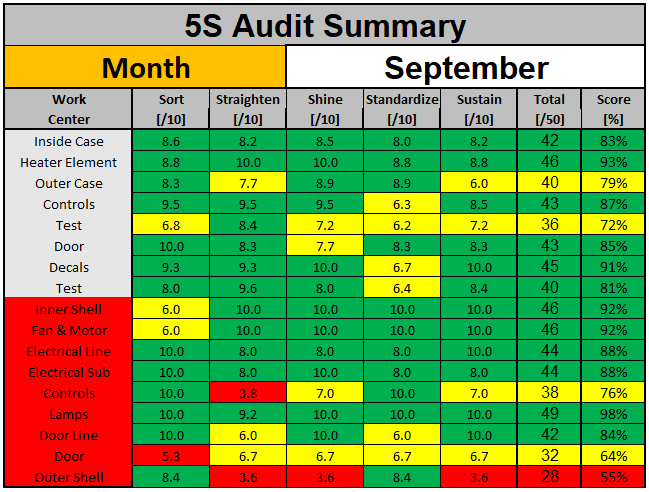
The example shows that work area 5 has a bad audit score and that this team will need help to get back to a GREEN level.
Step 5 - Promote Good Habits
Repetition is key when it comes to developing good cleaning and organizing habits. By consistently reminding someone to clean their work area, they will eventually start doing it automatically. Over time, any task that is repeated frequently will become a habit. If you work in a team, encourage each other to keep your work areas clean and organized. When your team members see you doing this, they will feel motivated to do the same, and it will become a habit for everyone. Keep up the good wor,k and continue to reinforce this habit in your team.
Step 6 - Promotes A Safe Work Environment
Sustaining the 5S methodology can provide an advantage in promoting a safer work environment. This is because with a cleaner work area, fewer hazards can result in accidents or injuries. For instance, if the floors are clean, the tools are properly stored, and the work areas are free of obstructions, then the chances of getting hurt would be significantly reduced.